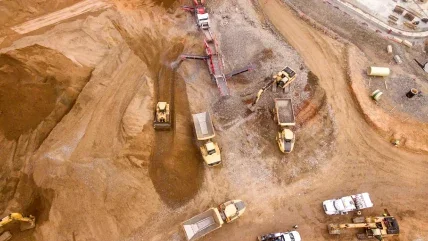
To date, much of the attention, investment and talent in autonomy has gone to on-road applications – particularly self-driving cars. While these innovations are exciting and hold the potential to reimagine how we get from Point A to B, they still face myriad challenges before they can be rolled out at scale – including mastering safety edge cases, overcoming significant red tape, and winning over the everyday commuter. But there is an opportunity for autonomy to have a meaningful impact today, off-road.
Since our start in 2017, SafeAI has been focused on delivering the benefits of connected autonomy to the construction and mining industries. Based in Milpitas, California, with another office in Perth, Australia, we retrofit heavy equipment such as dump trucks and skid steers, with autonomous hardware and software to help construction and mining companies create smarter, safer, more productive sites. While autonomous technology is not quite ready for the unpredictability of the open road, it is fully ready to operate safely and effectively in constrained environments. And heavy industry, particularly construction and mining, stands to benefit tremendously from implementing autonomy site-wide.
Right now, both construction and mining face labour shortages, dangerous conditions for workers, lengthening project delays, and ever-thinning margins. Autonomy directly addresses these problems by drastically improving productivity through 24/7 site operation, while simultaneously removing workers from direct interactions with potentially dangerous heavy machinery on project sites and allowing them to strategise and manage the site from afar. To provide a sense of impact, autonomy adds approximately 1000 hours of productivity per machine, per year, adding up to meaningful improvements in efficiency.
Ripe for innovation
Large-scale commercial construction projects, in particular—such as dam builds—are ripe for innovation. These projects are both time and labour intensive, and they include a tremendous amount of repetition. Load-haul-dump cycles, for example, are time-consuming and tedious, making them excellent candidates for automation. By introducing autonomy to keep sites running around the clock, a major project that used to take five years can now be completed in roughly three and a half years, allowing everyone to benefit from new infrastructure sooner.
To deliver autonomy, and its impact, at scale, SafeAI has taken a unique approach to deploying the technology. Many autonomous companies take a custom-build approach, creating self-driving equipment from the ground up; this is inherently inefficient and difficult to scale. What’s more, heavy industry has an abundance of equipment already—these industries don’t need more. At SafeAI, we’ve designed our business around a retrofit approach to autonomy, upgrading existing industry equipment rather than building new from scratch. Our approach is both OEM- and systems-agnostic, which means that any company that wants to modernise operations can work with SafeAI, regardless of what brand their fleet is. Already, SafeAI has retrofitted dump trucks, F150s, and skid steers with autonomous hardware and software. Ultimately, this approach lowers the historically steep barriers to entry for autonomy in construction and mining, and enables SafeAI to deliver autonomy faster, and at greater scale, than has previously been possible.
Our OEM- and systems-agnostic retrofit approach goes hand in hand with another core value at SafeAI: collaboration. We don’t believe any company can deliver autonomy industry-wide by itself, nor is it the most strategic or efficient approach. Instead, SafeAI has built an autonomous ecosystem that allows any industry player to integrate with our technology stack to create smarter sites and deliver autonomy project-wide. This allows us to play to our strengths without spreading ourselves too thin, while also ensuring our customers benefit from the best technology and expertise in the industry, site wide.
Recently, for example, we partnered with the Goodyear Tire & Rubber Company to deliver tire intelligence to autonomous heavy equipment. At SafeAI, we know tire health is critical to safe, efficient performance, and that any issues that arise can quickly cause costly downtime. But we’re not experts in tires; Goodyear is. By collaborating, we can focus on what we do best, building advanced, industry-specific AI to operate retrofitted fleets, while also offering our customers expertise from our partners.
Today, SafeAI and Goodyear can exchange site data on temperature, pressure, miles traveled and more to better understand equipment performance and identify potential problems – such as tire underinflation – before they have the chance to worsen and derail projects. This ecosystem approach is how we believe we’ll reach autonomy at scale faster and more effectively across the construction and mining industries.
In addition to our recent partnership with Goodyear, we also recently announced an agreement with the construction giant Obayashi Corporation to develop autonomous sites. Today, we have a pilot site in Cupertino, California, where a CAT 725 will soon be completing load-haul-dump cycles. Currently, SafeAI operates in the US and Australia, where each machine is exhaustively safety tested to understand optimal conditions related to weather, temperature, and more in order to ensure maximum safety. However, we plan to continue expanding globally to meet the rising need for connected autonomy in heavy industry, worldwide.
Covid-19
In fact, we’ve already seen interest accelerate in the last year. That’s because COVID-19, more than ever before, has highlighted the need for autonomous and digital solutions in the heavy equipment industry. As more project sites fall behind, and workers are faced with increasing health and safety issues, autonomy has emerged as a key competitive edge; wide-scale industry adoption is inevitable.
We believe that the industry is on the brink of a period of mass acceleration. The technology is ready, and it is proven. Now, it’s time we focus on rolling it out at scale to meet rising industry demand. The next few years will see an explosion in adoption; we plan to help lead the charge through our retrofit model and software ecosystem.
Ultimately, autonomy will make the jobsite of the tomorrow look very different than it does today. Right now, we tend to think of autonomy as taking over one machine to do a stand-alone task. But really, site-wide autonomy will allow us to think less about one piece of equipment, and more about how everything works together collaboratively to create a new workflow which is safer and more efficient than ever before. This approach will allow people to plan, direct and strategise in brand new, and much safer, ways to complete a project. Instead of looking at an excavator and seeing one machine, we’ll be able to see it for what it really is—just one cog in the machine building tomorrow’s newest dam.